Laser welding technology helps improve the quality of internal corner welding of stainless steel chassis
Stainless steel chassis is a common industrial equipment shell material, and its inner corner welding has always been a difficult problem in the manufacturing industry. However, with the continuous innovation and development of laser welding technology, today's laser welding machines have become a powerful tool to solve this problem. This article will introduce the application of laser welding technology in fillet welding of stainless steel chassis and its important role in improving welding quality.
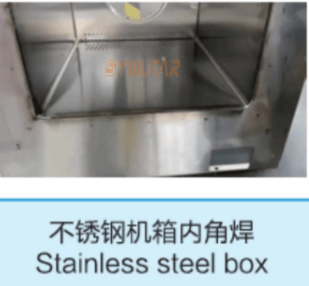
1. Challenges of traditional welding methods
In the traditional internal corner welding process of stainless steel chassis, traditional manual welding and traditional automated welding methods face a series of challenges because the internal corners are narrow and difficult to access. Common problems include welding defects, uneven welds, high deformation rates, etc. These problems will not only affect the quality and appearance of the welding, but may also lead to a decrease in the sealing and structural strength of the chassis.
2. Advantages of laser welding technology
Laser welding technology, with its high energy density, high precision and non-contact characteristics, has become an ideal choice to solve the problem of internal fillet welding of stainless steel chassis. Laser welding uses the focusing effect of the laser beam to concentrate high energy on the welding area, achieving refinement and efficiency of the weld. Compared with traditional welding methods, laser welding has the following advantages:
- Small weld width: Laser welding technology can achieve a very small weld width, thereby reducing the welding heat-affected area, reducing the deformation rate, and ensuring the accuracy and stability of welding.
- Fast welding speed: Laser welding technology has high energy density and high power output. The welding speed is much faster than traditional welding methods, which greatly improves production efficiency.
- Automated control: The laser welding machine is equipped with an intelligent control system, which can realize automated operation and real-time monitoring. Through advanced sensors and feedback mechanisms, laser welding machines can accurately control welding parameters to ensure the stability and consistency of welding quality.
3. Practical application cases
Currently, more and more manufacturing companies are using laser welding technology to solve the problem of internal corner welding of stainless steel chassis. Through the precise control of the laser welding machine and the focusing of the high-energy laser beam, the quality of internal fillet welding has been significantly improved. Welding defects are reduced, welds are uniform, and deformation rates are reduced, thereby improving the sealing, structural strength, and overall appearance of the chassis.
With the further development of laser welding technology, it is believed that the quality of internal corner welding of stainless steel chassis will usher in greater improvements. In the future, we can look forward to the launch of more intelligent laser welding machines, higher power and higher efficiency laser sources, and more advanced welding control systems. This will further increase the welding speed and accuracy, making the inner corner welding of the stainless steel chassis more perfect.
As an innovative solution, laser welding technology is bringing revolutionary changes to the internal fillet welding of stainless steel chassis. Through laser welding technology, we are able to overcome the challenges faced by traditional welding methods and improve welding quality and efficiency. With the continuous advancement of technology, laser welding technology will play an increasingly important role in the manufacturing industry, promoting the innovation and development of the manufacturing industry.v